The project started in December 2017, when EcoBunker construction manager Llewelyn Matthews travelled to Guernsey to build a test bunker on the club’s short game practice area. The success of this trial project convinced Royal Guernsey to sign up for a three-year project to rebuild all 31 bunkers on the course, as well as adding some new fairway traps in the last phase, which will begin in winter 2020-21.
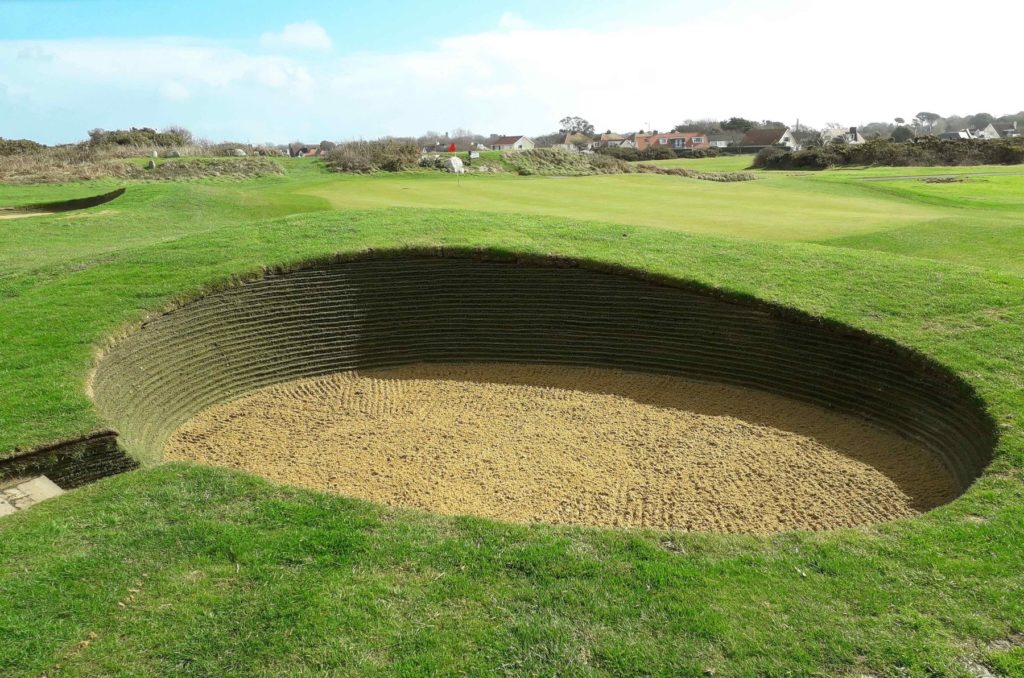
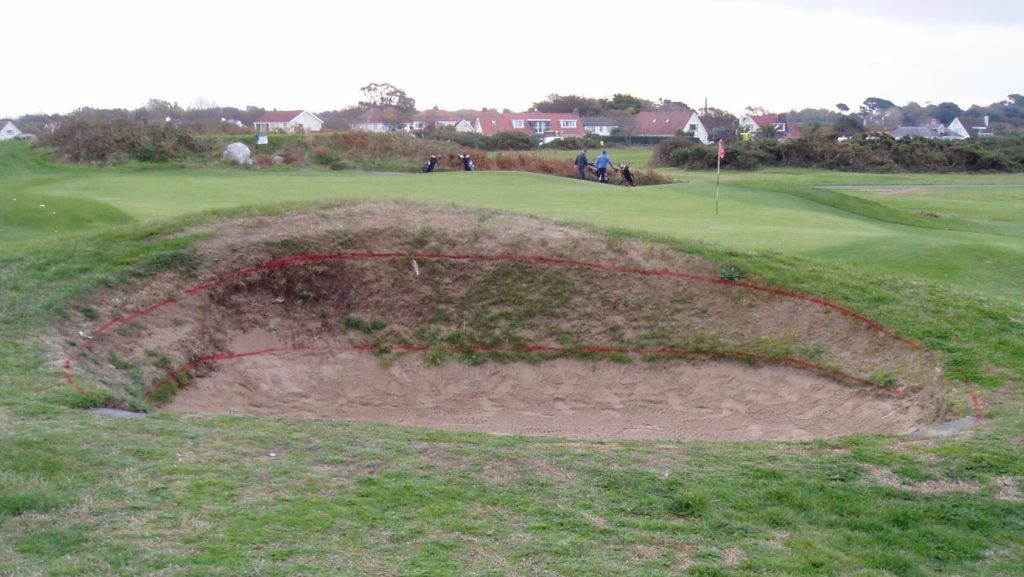
Matthews returned to the L’Ancresse links – also home to the L’Ancresse Golf Club – in November last year for a refresher training exercise. Course manager Marcus Hamon says: “These bunkers needed to be right, as they would be around for a long time. Llewellyn didn’t let me down, and the rebuilt bunkers look great and sit nicely in the undulations of the course. The service from Richard and the team at EcoBunker was first class from the very first telephone call to the end of phase one, and I’m looking forward to working with them on phases two and three.”
Hamon added: “The members of the golf club are delighted with the 15 bunkers that have been rebuilt so far. The bunkers at L’Ancresse have been a weak area for a number of years, and the new EcoBunkers have totally transformed the course.”
EcoBunker CEO Richard Allen said: “All of us at EcoBunker are delighted at the superb bunker work being undertaken by Marcus and his dedicated team at L’Ancresse Links. The success of the Royal Guernsey project is a testimony to the effectiveness of our EcoBunker Advanced process, which reduces the weight of turf required to build a bunker by the use of cantilevering and a cement modified backfill. This both strengthens the bunker wall, and dramatically reduces the shipping costs of the product. Had we been forced to use our original method, with wider tiles of artificial turf, the shipping to Royal Guernsey would have required two full trucks. Instead, we only needed one – representing a saving to the club of £2,500 just on the first phase of the project.
“The best engineering solutions deliver the required outcomes while avoiding environmental impact, use of resources and minimising cost,” added Allen. “My original invention was good in many, many respects, but as it was very heavy, as soon as we began exporting around the world I recognised the need for ‘value engineering’. VE was one of my principal responsibilities whilst working as a technical director in a civil engineering consultancy. Weight adds considerable shipping cost, so I designed a far more efficient solution, which we call EcoBunker Advanced.“